SAY Plastics
Resources
Thermoplastic Resources
Check out Company News, Industry Insights, and Videos!
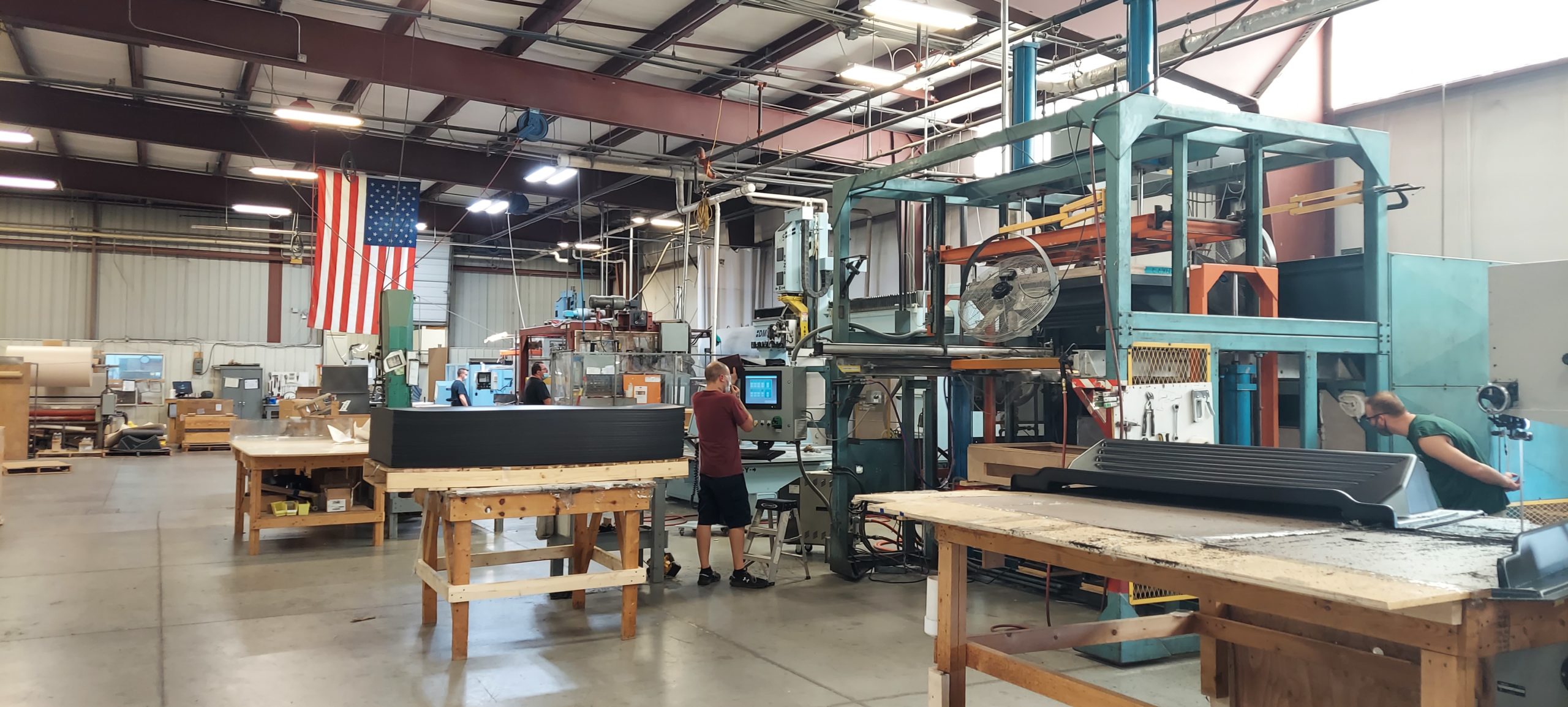
Lets Collaborate To Provide You a Competitive Edge!
Our Passionate Team Is Eager To Get Started
Schedule a ConsultationSAY Plastics
Check out Company News, Industry Insights, and Videos!
Our Passionate Team Is Eager To Get Started
Schedule a Consultation