The disposable nature of the packing materials created waste, while additional time was needed to inspect and pack pallets for return to the supplier. The pallet weight required two workers for the handling process, and injuries from nails and splinters were common. Due to the ineffectiveness of the material handling system, wheel scuffs and scratches often occurred.
In order to support their LEAN the motorcycle plant needed to find a way to cut the waste, decrease manpower, and improve the safety of their current material handling process. So they turned to SAY Plastics for help.
When the manufacturing engineers contacted SAY to discuss the project, SAY welcomed the challenge. By re-thinking the design of the current system and exploring ways to use thermoformed materials in place of the existing materials, SAY engineers were able to design and develop a unique handling system featuring custom thermoformed tray dividers, plastic pallets, and protective top caps.
The system that SAY engineered uses multiple components that work together to create one impressive final product. SAY first developed a method for permanently adhering a closed-cell foam into the tray divider wheel location during the forming process.
SAY then developed a smart interlock feature that allowed the dividers to lock for a secure transport. Wood pallets were replaced with plastic pallets. The final piece was a top cap that protects the wheels and is secured with a strap mechanism that is permanently affixed to the system.
Working with SAY Plastics gave this world class manufacturer the results they were looking for – less waste, greater efficiency, improved safety, and better quality. And SAY’s material handling solution paid for itself in less than five turns.
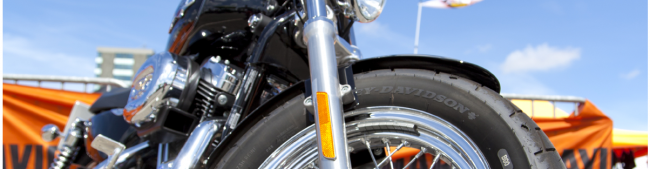