A few years ago, Stone Mountain expanded their popular snow tubing attraction by introducing the Double Tube which allows two people to ride the hill on a single tube. Unfortunately, the Double Tube received lackluster reviews by park goers. “Less-than-thrilling rider experience” was the verdict. Full Spectrum’s tube supplier was unsuccessful at producing a double snow tube pan, which is the part configured to the bottom of the tube that ensures optimal tube speed and performance under varying snow conditions.
A new double snow tube pan configuration was proposed by the tube supplier, but it was costly and would extend the manufacturing schedule. In addition, the new configuration would lower the tube’s speed and jeopardize tube durability.
Full Spectrum and Stone Mountain tested different Double Tube pan options over the years, including using a tarpaulin bottom on the tube. The trials brought disappointing results. As they ramped up for another winter snow season in September 2016, Full Spectrum and Stone Mountain were determined to find a no-fail solution that would deliver a consistently remarkable tubing experience and increase revenue for the company. Enter SAY Plastics, a custom Thermoformer in Pennsylvania.
Full Spectrum and Stone Mountain reached out to SAY Plastics in September at the recommendation of another supplier. SAY Plastics was tasked with developing a pan solution and delivering 170 pans in time for 2016/2017 tubing season. SAY Plastics determined they could thermoform the pan from an economical polyethylene material. Instead of sewing the pans onto the snow tubes, which was the assembly method for the single tubes, SAY Plastics designed a new assembly that utilized mechanical fasteners with pan head bolts.
The SAY Tooling System allowed SAY Plastics to quickly set up the forming, trimming and assembly process which delivered significant cost savings. SAY Plastics turned to CMT Materials in Attleboro, Massachusetts to provide materials for their inhouse tool construction. CMT recommended using their HYTAC® LPX syntactic foam material for the mold. Due to the unique properties of syntactic foam, including low thermal conductivity, the tool quickly dissipates the heat from the thermoforming process. This results in a more stable and repeat-able process and delivers uniform parts. CMT Materials produced a solid cast mold block which both prevented delamination issues and allowed for no seams and less prep work than traditional composite board molds. SAY Plastics could CNC-machine the finished mold and then construct a plywood and steel CNC trim fixture in-house.
In less than 8 weeks, SAY Plastics delivered the quote, design, tooling, thermoforming and assembly of the complete customer order. Due to the aggressive schedule and a few unknown factors in the project, SAY provided an initial target price for the project but was ultimately able to offer a discount on the final cost thanks to the cast syntactic from CMT Materials and the machining and assembly savings made possible by their SAY Tooling System.
The new Double Tube pans were a success and the project management team at Full Spectrum says response to the tubes has been positive. “The tubes are working great and have quickly become a popular choice with riders.”
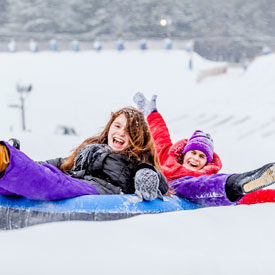